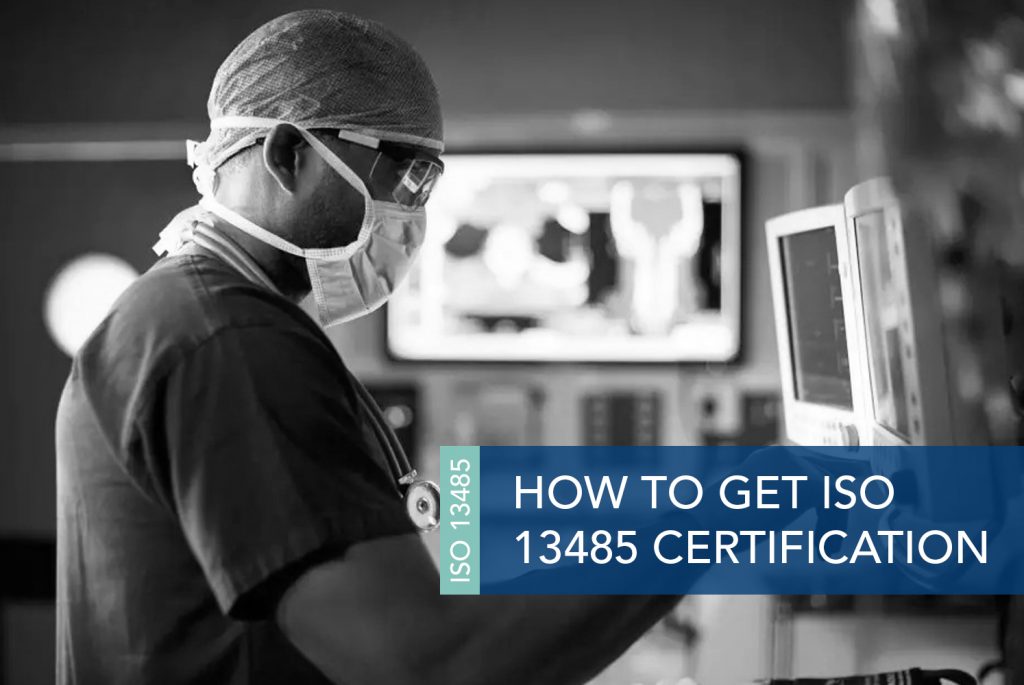
How to get ISO 13485 certification
March 31st, 2021 By AmywrightIf you’re a medical device manufacturer, it’s likely that ISO 13485 will be on your radar. This internationally-recognised standard ensures such vital technology as yours is safe, effective and delivered to a high quality. Not only does the certification help you become compliant with national and international legal requirements, but it will also help to open your business to a global market. Here’s how to become ISO 13485 certified.
What is ISO 13485?
ISO 13485 is a type of Quality Management System (QMS) for organisations that provide medical devices. Anyone in the industry knows that your product needs to consistently meet client and regulatory requirements – a service that has become even more vital in the wake of the global coronavirus pandemic.
ISO 13485 is the most accepted global standard of its kind and comes with a wealth of advantages. The benefits of ISO 13845 include:
- Getting up-to-date with the needs of regulatory authorities
- Confidence to establish your business in the global market
- Establishing robust control processes, including product development, manufacture and distribution
- Optimised efficiency which leads to minimised costs
- Gaining control of your supply chain
Is ISO 13485 mandatory?
In a nutshell, no, ISO 13485 is not mandatory, however, certification is extremely important as it harmonises your practices with legal and regulatory requirements that exist across the country, the EU and the rest of the globe. While not mandatory, an organisation may find difficulty operating in some markets or getting their product recognised without it. Like most ISO standards, the framework is flexible, and you can build a QMS for medical devices that suit your organisation as long as it meets international standards.
How to get ISO 13485 certification?
Many medical device manufacturers find that expert consultants can help them implement their ISO 13485 QMS with ease. With IMSM, our consultants work with you to design your QMS and design control requirements, before submitting your organisation to a recognised certification body to audit your business and get you ISO 13485 certified.
ISO 13485 requirements are applicable to any organisation, no matter the size or complexity, including services as well as products. The structure of the standard consists of eight sections: the first three are introductory, and the final five contain details of the requirements for compliance for medical device manufacturing. The five main sections are as follows:
- Section 4: Quality Management System – discussing the QMS and documentation requirements
- Section 5: Management Responsibility – outlining how management is responsible for the success and maintenance of the QMS
- Section 6: Resource Management – detailing how human resources, buildings, infrastructure and the working environment need to be controlled
- Section 7: Product Realisation – dealing with how to plan, review, design, purchase, create, control and measure your product
- Section 8: Measurement, Analysis and Improvement – covering how to monitor your QMS’ success, taking into account essential measurements like customer satisfaction, internal audits and corrective and preventive actions.
The next step involves operating your newly-implemented QMS so you can collect the necessary documentation to audit, review your system and receive certification. These steps are as follows:
- Performing an internal audit to ensure all the necessary processes are in place and identify any weaknesses that could cost you certification
- Management conduct a formal review to evaluate decision-making and resource assignment
- Use the above tasks to identify problems, correct them and document how they were resolved
If you want to know about ISO 13485 and the certification process, click this link!
Contact Us
For a free Quotation or On-Site presentation by an ISO Specialist, contact us today!
IMSM New Zealand Ltd.
Level 33, 23-29 Albert Street,
Auckland Central,
Auckland -1010,
New Zealand